Types of Die Attach Adhesives
Published date: 26 November 2023
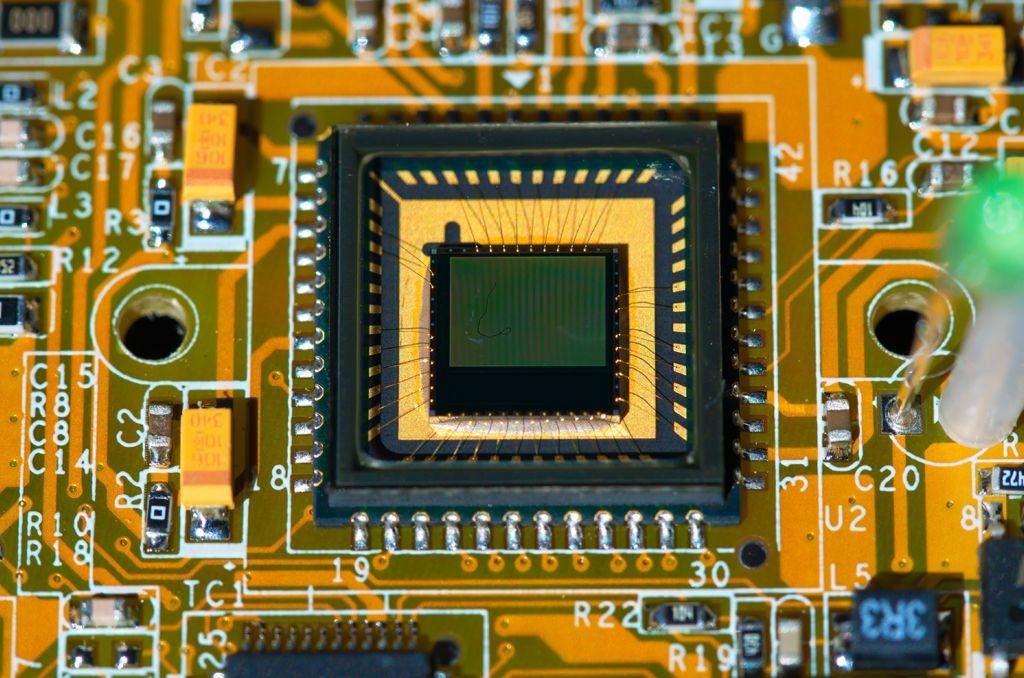
Die attach adhesives are used to bond silicon chips to the substrates of semiconductor packages, playing a pivotal role in the performance of electronic components. Choosing the appropriate die attach adhesive is a critical decision, influencing the stability, conductivity, and insulation of these devices. In this guide, we will explore the various types of die attach adhesives, shedding light on their characteristics, applications, and the scenarios in which they shine.
Epoxy Adhesives
One of the most common types of die attach adhesives is epoxy. Renowned for their versatility, epoxy adhesives provide a robust and stable bond. Composed of two parts, resin and hardener, epoxy cures to form a durable, rigid structure. Its ability to resist thermal and mechanical stresses makes it a popular choice for semiconductor applications. The curing process in epoxy die attach is crucial: inadequate curing may result in a weak bond, while excessive curing can render the adhesive brittle and prone to cracking.
The main advantage of epoxy adhesives lies in their adaptability. Formulations can be tailored to various applications, such as high thermal conductivity for heat-sensitive scenarios, or low-outgassing properties suitable for vacuum environments. Epoxy die attach adhesives find their niche in applications where stability and reliability are paramount, such as in the assembly of integrated circuits and power devices.
Electrically Conductive Adhesives
Electrically conductive die attach adhesives, often based on silver-filled polymer resins, are used in die bonding applications requiring electrical conductivity. Their ability to bridge the gap between components while maintaining conductivity positions them as a go-to solution for a range of semiconductor applications. These include semiconductor assembly onto lead-frames, microelectronic hybrid assembly onto alumina, and high-reliability devices.
Electrically conductive die attach adhesives, particularly for leadframe and laminate wire bond packages, meet stringent application-specific processing and performance requirements. A diverse range of adhesive formulations caters to the demands of today’s electronics. Polymer resins like epoxies, maleimides, bismaleimides, acrylates, silicone, cyanate esters are commonly used in conductive die attach adhesives. Typical conductive fillers include silver, gold, copper and nickel.
Non-Conductive Adhesives
In contrast to their conductive counterparts, non-conductive die attach adhesives are tailored for applications where electrical insulation is paramount. Utilizing a range of non-conductive fillers like silica, alumina, aluminium hydroxide, mica and glass, these adhesives provide electrical insulation crucial for circuit integrity. Optoelectronic devices and sensors often benefit from the insulating properties of non-conductive adhesives, preventing unintended electrical contact and offering a protective shield for fine-pitch devices. These adhesives are also employed for their thermally conductive properties, making them ideal for bonding heat-dissipating components to heat sinks.
Click here to view all die attach adhesives.
At Conro Electronics, we’ll show you how to improve product reliability while increasing performance and lowering costs. Our team of technical support specialists will provide your company with dependable global supply, unrivalled efficiency, and superior technical support.
Feel free to contact us on 0208 953 1211 or send us an email to info@conro.com
Comments
There are currently no comments, be the first to comment.