What is aerospace adhesive?
Published date: 27 December 2021
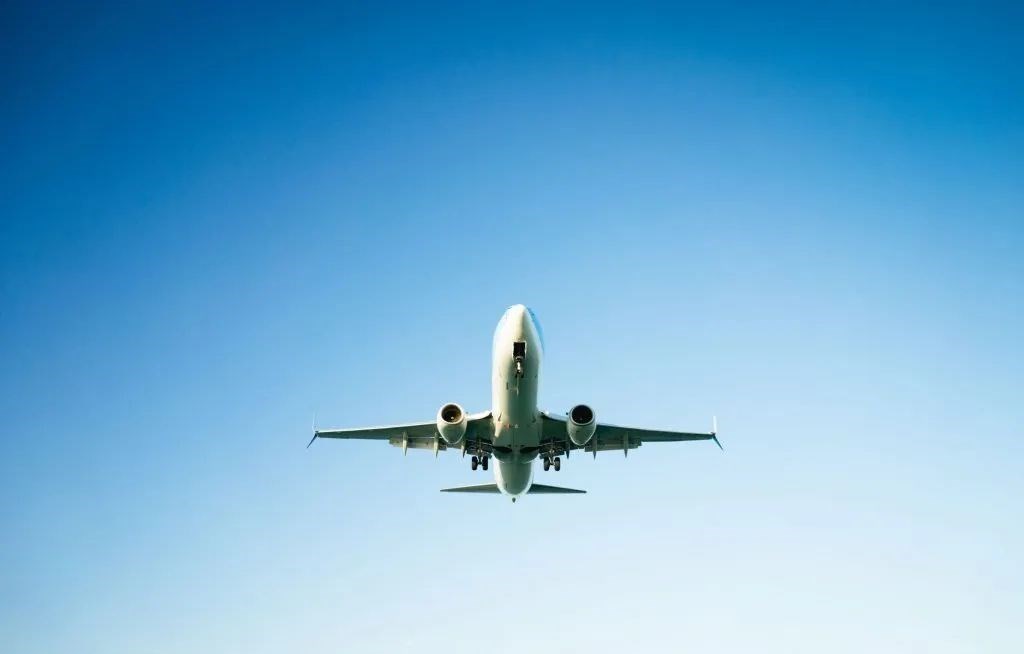
Aerospace adhesive is adhesive used in aerospace applications. These cover the interior, exterior and engine compartment of an aircraft. Adhesive applications range from thread locking, to retaining. From gasketing to thread sealing, and more.
Adhesives improve stress distribution over bonded joints. They protect against corrosion and enhance aerodynamics and aesthetics. Using adhesive lowers aircraft weight. It saves time and money. Select grades will resist even extreme operating environments.
What adhesives are used in aerospace applications?
Anaerobics, structural acrylics, epoxies, cyanoacrylates are all common. Adhesive tapes and films are also frequently used.
The properties of adhesives are tailored to the needs of the aerospace industry. Additives are used for altered viscosity, increased toughness, shorter cure time, and more. Special flame-retardant products have been developed for interior applications.
- Anaerobic adhesives: Anaerobics, such as retaining compounds, see most of their use in the engine compartment. Threadlockers, however, are used throughout the aircraft. Their action prevents loosening of components from vibration.
- Structural acrylics: Used in many different applications. Examples include bonding magnets into electric motors and attaching harness clips. An adhesive is considered structural if it can withstand 1000 psi of shear force.
- Epoxies: The dominant aerospace adhesives. Widely used for their strength and low density. Epoxies are used as honeycomb edge fillers for bonding composites. Their reduced weight helps keep the aircraft as light as possible.
- Cyanoacrylates: Used to instantly hold parts that are being bonded with slower adhesives. Also used by themselves. Useful as quick fixers for damaged interior coverings.
Aircraft parts require high quality adhesives. Compliance to specifications guarantees product reliability. Examples would be AS 9120 or Military Specification. Companies such as Boeing or Lockheed Martin have proprietary specifications.
How are aerospace adhesives used?
Adhesives for aerospace use are typically applied in the form of paste or film. Pastes fill gaps between surfaces with thick bond lines. This guarantees better resistance. Adhesive pastes are easy to apply and excellent for use on vertical surfaces. They are suited to bond both composites and metal.
Films, consisting of a thin layer of resin, are available in ready-to-use roll or sheet form. They cure fast at moderate temperatures. Their adhesive strength is outstanding. Films are available in a range of thicknesses and weights. They are used to bond large areas of composite parts. Specialised films are designed for lightning strike protection.
Surface preparation is critical when using aerospace adhesive. This is especially true for composite bonding. Many aerocomposites employ peel ply, a release fabric cured with the part. Peeling it off after curing abrades the top layer without damaging fibers. This enhances surface energy for adhesive bonding. Hand or machine abrasion is also used.
Conro Electronics, as an electronic manufacturing distributor, offers a wide choice of adhesives suitable for aerospace use, from major manufacturers such as Henkel Loctite.
We’ll show you how to improve product reliability while increasing performance and lowering costs. Our team of technical support specialists will provide your company with dependable global supply, unrivalled efficiency, and superior technical support.
Feel free to contact us on 0208 953 1211 or send us an email to info@conro.com
Comments
There are currently no comments, be the first to comment.