Die Attach Process
Published date: 06 November 2023
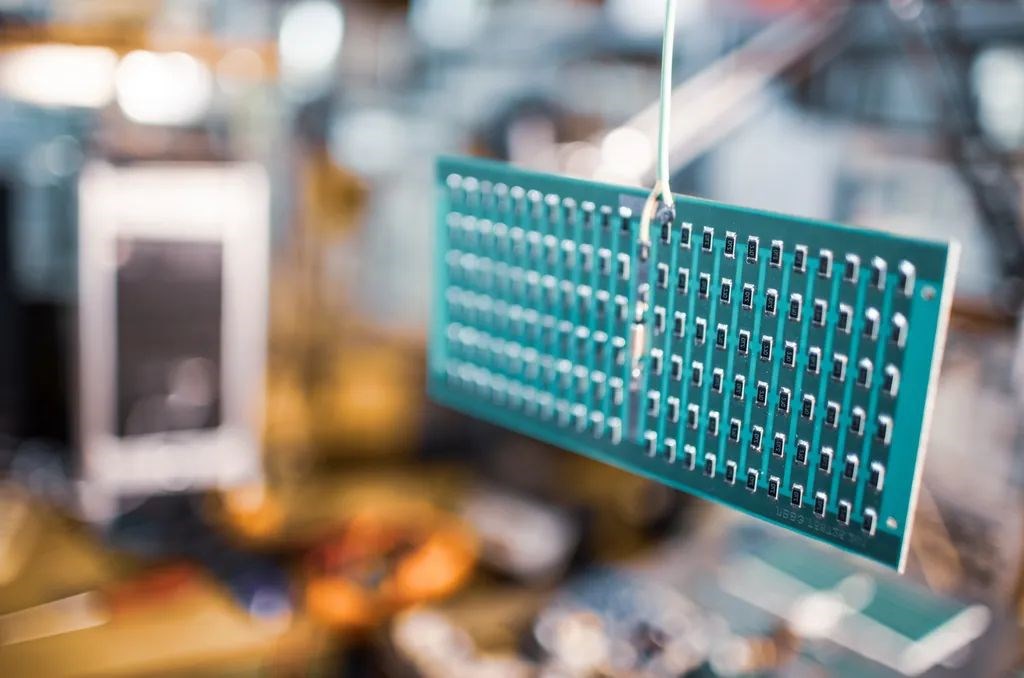
The die attach process is a crucial procedure in semiconductor manufacturing. The term describes the process of bonding a semiconductor die onto a substrate or package, such as a lead frame or PCB. There are two predominant types of die attach methodologies: eutectic and adhesive. In this blog post, we are going to focus on the latter, encompassing substrate preparation, adhesive dispensing, die placement, and the crucial curing phase.
Substrate Preparation
Prior to die attach, careful substrate preparation is essential to achieve a flawless bond. The substrate’s surface must be free from contaminants that could compromise the adhesive’s efficacy. The cleaning procedures usually involve solvent-based products or ultrasonic cleaning using aqueous fluids. Additionally, surface treatment methods are performed to enhance substrate wettability, facilitating optimal adhesion strength. Typical surface treatments include plasma cleaning, laser ablation and corona treatment.
Adhesive Dispensing
The application of die attach adhesive plays a pivotal role in the overall success of the process. Die attach adhesives can be applied by dispensing, jetting, stamping, or screen/stencil printing. The characteristics of the adhesive, such as viscosity and susceptibility to moisture, will usually dictate the application method. Automated dispensing systems ensure accurate and uniform distribution of the adhesive, mitigating the risk of uneven bonding. The most common systems used in the die attach process employ a time pressure dispensing valve, auger pump, positive displacement pump, or a jetting valve. Each technique provides its unique benefits and drawbacks.
Die Placement
To ensure the utmost precision and accuracy, automated pick and place machines are used to position the semiconductor die onto the adhesive-coated substrate. As the die is placed, the adhesive spreads to cover the die attach pad. The alignment must be flawless, to ensure optimal functionality and longevity of the final semiconductor device. Any misalignment at this stage could lead to compromised performance, rendering the entire manufacturing process futile.
Curing
The curing phase is where the die attach process transforms into a robust bond. Temperature and time profiles during curing dictate the die attach adhesive’s curing kinetics, influencing the bond’s strength and stability. Achieving the right balance is imperative. Insufficient curing time or inadequate temperature can result in an under-cured bond, leading to compromised mechanical and thermal properties. Conversely, excessive curing time or elevated temperatures may cause thermal degradation, impacting the adhesive’s efficacy. Striking the optimal balance ensures that the adhesive cures uniformly, achieving the desired properties without compromising the semiconductor’s integrity.
After Curing
Once the die attach process is complete, the desirable qualities of cured die attach adhesive are as follows:
- Thin bond line: A thin bond line is a crucial factor in minimising both electrical and thermal resistance.
- Void-free: To maximise strength, thermal conductivity, and electrical conductivity, adhesion bond lines should be void-free, avoiding any cracks and air bubbles.
- No squeeze-out: The cured adhesive must not squeeze out and make contact with adjacent bond pads. This precaution is especially vital when employing electrically conductive adhesives, as inadvertent contact could lead to electrical shorts.
At Conro Electronics, we’ll show you how to improve product reliability while increasing performance and lowering costs. Our team of technical support specialists will provide your company with dependable global supply, unrivalled efficiency, and superior technical support.
Feel free to contact us on 0208 953 1211 or send us an email to info@conro.com
Comments
There are currently no comments, be the first to comment.