Die Attach Adhesives – Quality Control and Testing
Published date: 12 March 2024
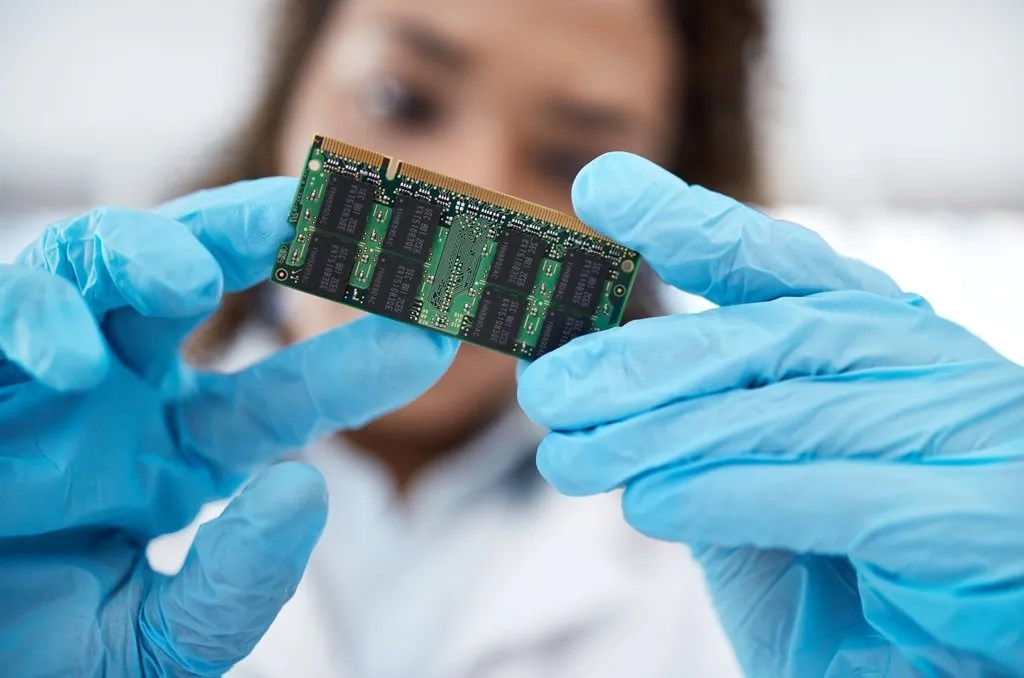
Die attach adhesives provide a reliable alternative to eutectic die bonding in semiconductor manufacturing, ensuring the secure attachment of semiconductor chips to substrates or packages. Quality control measures and rigorous testing protocols are imperative to ascertain the reliability and performance of these adhesives.
Understanding Die Attach Failure Mechanisms
Quality control of die attach adhesives is founded on understanding the various failure mechanisms that can compromise the integrity of the die/substrate bond. These mechanisms include die lifting, die cracking, and adhesive contamination.
- Die lifting is the partial separation of the die from its substrate. It occurs when there is incomplete coverage of the adhesive or the formation of voids during deposition.
- Die cracking refers to physical damage to the die. It can result from excessive die ejection force when separating a die from the substrate, or from uneven adhesive coverage.
- Adhesive contamination, where the adhesive climbs the die edges, can lead to short circuits and functional failure, especially with conductive adhesives. This highlights the importance of precise dispensing techniques to prevent excess adhesive volume.
Testing Die Attachments for Reliability
Die attach adhesives undergo rigorous testing to evaluate their strength and reliability under real-world conditions. Several testing methodologies are employed.
- Die shear tests involve applying a force parallel to the substrate to determine the adhesive bond strength. The application of force will produce a range of failure mechanisms, which indicate the strength of the die bond.
- Die pull tests assess the bond integrity by pulling the die away from the substrate, observing whether the die breaks off or incurs physical damage.
- Thermal testing is crucial for assessing the adhesive’s ability to withstand temperature extremes or thermal cycling. This type of testing can reveal potential failure modes, such as die lifting or substrate bond failure.
A particular type of thermal testing is used to measure the thermal conductivity of die attach adhesive. This property is essential for applications requiring efficient heat dissipation, such as power electronics for hybrid cars. In 2012, researchers at the EPFL Microtechnical Production Laboratory have developed a viable testing method for epoxy die attach adhesives used in high temperature applications. The process involves heating a mock die and then cooling it off, with the time constant of the temperature decay measured to calculate the thermal conductivity of the adhesive.
Failure Analysis Techniques
In the event of adhesive bond failure, thorough failure analysis is necessary to pinpoint the root cause and implement corrective measures.
- Techniques such as microscopy and spectroscopy enable detailed examination of the bond interface and identification of defects or contaminants.
- Chemical analysis techniques help determine the composition of contaminants, facilitating targeted mitigation strategies.
- Finite element analysis (FEA) aids in simulating mechanical stresses and predicting failure modes, guiding design improvements for enhanced reliability.
At Conro Electronics, we’ll show you how to improve product reliability while increasing performance and lowering costs. Our team of technical support specialists will provide your company with dependable global supply, unrivalled efficiency, and superior technical support.
Feel free to contact us on 0208 953 1211 or send us an email to info@conro.com
Comments
There are currently no comments, be the first to comment.